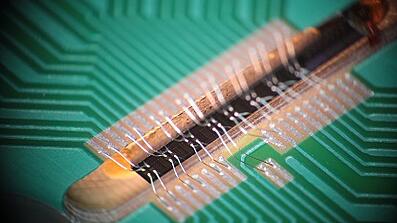
Using a few simple techniques can help ensure a more robust printed circuit board design which can also help you save money.
Printed circuit board design is a balance between functionality, longevity, aesthetics and board costs, time to design and the PCB fabricators capabilities. Listed below are eleven of the most common best practices we recommend to our customers.
$ - Circuit Board Thickness to Drill Diameter Ratio: Cost can be reduced by keeping the PCB thickness to drill diameter ratio less than 3.9:1
For example, a 0.062” thick board with a minimum drill size of 0.020” results in a ratio of 3.1:1 which will not incur extra costs.
$ - Best Practices - Annular Rings: On small holes, ensure annular ring widths are at a minimum of 0.005”. The recommended annular ring size is 0.006” and greater. We also recommend designing the annual ring in the shape of a droplet, particularly when the minimum width of 0.005” is used.
$ - Drill Hole Count: Hole counts of more than 40 drilled holes / square inch will increase the price of your PCB.
$ - Best Practices - Trace Angles: Designing with angles greater than 90 degrees can enable acid traps which can be harmful to the circuit board. Utilizing 45 degree angles are suggested as they have a smaller impact on the width of the Trace. Narrow angles can cause electromagnetic radiation and copper migration over time and should be avoided.
$ - Space and Trace: When current and space is not an issue, we recommend spaces and traces, dependent on copper thickness, that are equal or greater than:
- 0.007”/0.007” for 1/2 oz Cu boards
- 0.008”/0.008” for 1 oz Cu boards
- 0.010”/0.010” for 2 oz Cu boards
- 0.012”/0.012” for 3 oz Cu boards
Designs with specifications less than 0.007”/0.007” will incur higher costs. It is also recommended to keep the space between a Trace and the ground plane at a minimum of 0.008”, but a space of 0.010” is preferred.
$ - Best Practices - Ground Plane: When specifying V-scoring, ensure the ground plane is at least 0.020” from the edge of the circuit board. For routed boards ensure 0.010” between the ground plane and the edge of the circuit board.
$ - Plated Slots: Specifying plated slots when they are not required will result in higher than necessary board costs. There are no extra charges for unplated slots.
$ - Best Practices – Solder Mask: We recommend solder mask on all boards. The savings from omitting the solder mask are slight and the risk of short circuits in the soldering process are much greater. It is acceptable to put solder mask over through-hole vias. It is recommended to provide zero mask expansion and allow your PCB fabricator to adjust as needed.
$ - Silkscreen: Line resolutions of 0.008” and font heights of 0.040” require the additional process of exposure and developing. It is recommended to keep the minimum line resolution at 0.010” and font heights at 0.060”.
$ - Best Practices – Routing: The standard separation between boards is 0.100”. The position, width and hole patterns for breakout tabs can be provided but unless specifically requested, they may be edited for improved manufacturability.
$ - Change Control: Ensure your documentation contains a Revision letter/number and maintain the revision when changes occur. Undocumented changes are a leading cause of errors resulting in the loss of whole orders. It is also good practice to provide the part number and version/revision to either the silkscreen or copper layers.
$ - Although the best time to implement these techniques is at the design stage, depending on the volume and expected lifespan of your product, you may be able to get payback with a DFM redesign. Often, the simplest method to determining the feasibility of a redesign is by working directly with your PCB fabricator, reviewing their manufacturing capabilities and simply being open about your design requirements.