The problem when soldering to Aluminum
Aluminum reacts very quickly with oxidizers in the air. It immediately develops a passive layer of aluminum oxide surrounding the pure metal, making it difficult to solder than copper.
The first section of this post touches on the basics of soldering to achieve proper wetting, which does not change regardless of soldering to aluminum or copper. Feel free to skip this part if you already know the basics.The second section explains how to solder NbTi copper-coated wire to an aluminum pad in a PCB and manually create superconducting solder joints.
Section 1: The basics of soldering in electronics
Soldering flux materials include:
- Liquid flux
- Paste flux
- Solder paste (also called solder cream)
- Solder powder (made to order)
- Solder preforms (off the shelf and made to order)
- Solder spheres
- Flux-coated, flux-cored, or both solder ribbon
- Flux-coated, flux-cored, or both solder wire*
- Fluxed and non-fluxed solder bars
*Solder wires are like tubes that release liquid flux and are generally available in wire sizes (outside diameters) of 0.25 mm (0.00984 in) to 4.75 mm (0.187 in).
According to their composition, flux type, and physical form, the flux manufacturers' responsibility is to classify their fluxes per IPC J-STD-OO4 standard.
The solder alloy manufacturer's responsibility is to qualify their solder alloys as per IPC J-STD-OO5 and IPC J-STD-OO6 standards.
Flux Know-How
Flux is the material that breaks down surface oxides present on the surfaces to be wetted, i.e. PCB pads and component leads. Think of it as a soap that will help clean the area to be soldered. Flux's second main task is to prevent oxidation of the surfaces during heating. The third main task (and most important for soldering to aluminum) is to promote good wetting and solder spreading by lowering the surface tension and assisting in heat transfer from the heat source to the item being soldered, which is especially critical for hand and pulse soldering.
Flux composition is based on its nonvolatile portion's largest weight percent constituent and can be either rosin (RO), resin (RE), organic (OR), or inorganic (IN). The old flux classifications of R, RMA, and RA have been phased out.
- RO fluxes are based on material obtained from pine trees and conifers. These are mild fluxes that leave a relatively inert residue that isn't corrosive when used as paste flux or in flux-cored wire solder.
- RE fluxes are based on synthetic or modified rosins called resin. These are also mild fluxes but have better thermal stability and could be modified so that their residues are easier to clean.
- OR fluxes are based on organic acids and salts. These are very active fluxes that absorb water from the environment, increasing their quantity and mobility. Knowing that neutralizing of flux requires heating to soldering temperature, their use is not recommended in areas where flux can be trapped, like in stranded wires.
- IN fluxes are based on metal chloride salts. These fluxes are highly corrosive and not wholly removable with a water rinse.
Flux activity is based on its residues' ionic and corrosive activity. It is the ability of the flux to reduce oxides and protect the surfaces from re-oxidizing.
Flux type is based on its activity, halide* content and its residues' corrosive or conductive properties. It defines the impact of the flux residues on the long-term reliability of the assembly or device to be soldered. According to these, flux type classification is as follows (where 0 or 1 indicates the absence or presence of halide):
- L, 0 or 1 = Low or no flux/flux residue activity
- M, 0 or 1 = Moderate flux/flux residue activity
- H, 0 or 1 = High flux/flux residue activity
*Halogens left on the board will convert tin, silver and exposed copper into metal salts over time.
No-clean fluxes may have rosin (RO), resin (RE) compositions, or almost free rosins and resins, in which case they are classified as organic (OR). They typically have type L or M activity levels.
Water-soluble fluxes generally have organic compositions (OR), and they typically have type H activity levels.
Solder Know-How
Solder paste is the material that provides a wetted solder connection between solderable surfaces and is made of:
- Flux (explained above)
- Solder powder alloy
Solder powder is the name given to small spherical particles of solder. Solder alloys with smaller powder sizes are more prone to oxidation. Molten solder will only flow out and bond to clean metal surfaces. When dispensing solder through a needle or syringe, large powder sizes can create blockages.
Eutectic and non-eutectic solder alloys have both a solidus and a liquidus temperature. For the non-eutectic alloys, there is a plastic melting range between the solidus and liquidus state; however, for the eutectic alloys, the melting of the solder occurs at a given single sharp temperature. The use of eutectic solder is preferred for SMDs because it promotes rapid solidification of the solder connections, minimizing grain growth, yielding shinier solder joints and decreasing the occurrence of disturbed solder connections, which occasionally results in a rough surface and dewetting.
Special doped solder alloys contain additives that are not fully disclosed. You would need to contact the solder manufacturer for any technical datasheet required.
Intermetallics: When solder bonds or "wets" to metals, a metallurgical reaction occurs between the solder and the base metal, this reaction creates a new metal alloy known as intermetallic. This intermetallic layer holds the solder connection together. The intermetallic thickness and quality are driven primarily by dwell time and temperature.
In the end, wetting of a solder paste is dependent on the following factors: PCB surface finish, component metallization, reflow profile (dwell time and cooling rate), solder alloy and flux.
Manual/Hand soldering tools and equipment include:
- ESD mat, wristband and gloves
- Preheater
- Static solder pot
- Soldering iron and soldering tips (We recommend Metcal soldering tools and equipment for process control and reduced dwell time)
- Sulphur-free sponge damped with deionized water
- Brass pad
- PCB holder/vise
- Microscope
Section 2: Recommendation on how to solder NbTi copper-coated wire to an aluminum pad and manually create superconducting solder joints in a PCBA
When heating the solder paste above the melting point of the solder alloy it contains, the alloy particles should merge to form one volume of metal.
The flux incorporated in the solder must have sufficient fluxing action to secure the complete coalescence of the solder particles and enable the molten solder to wet the aluminum pads.
Therefore the pads and component leads or wire must be as free from oxide as possible to obtain the maximum efficiency of the flux contained in the solder. This flux must have as low aggressiveness as possible yet be strong enough to aid in the solder joint formation.
Solder considerations: The best conductors at room temperature (gold, silver, and copper) do not become superconducting at low temperatures. 63/37 tin/lead solder alloys are better suited for surface mount devices because of the better capillary action of their eutectic alloy compared to the non-eutectic 60/40.
Flux considerations: Both the flux within the solder paste and the external flux used in conjunction must be compatible from a cleaning process standpoint and a chemical standpoint. Refer to IPC-9202 and IPC-9203 for examples of qualifying testing. Electrical leakage, metal migration and corrosion are most likely to occur with liquid flux because it tends to spread to other areas and may not reach full activation temperature.
PCB Finish considerations: Our PCBs do not have a finishing process. Aluminum surface and "selective copper over aluminum" are the only metal options if you want to achieve superconductivity.
Prepping considerations: We suggest precleaning the pads, component leads and wire to remove fingerprint oils, grease and dirt. The remaining oxide on these will be taken care of by the flux.
Select the soldering tip with the largest possible contact area relative to the size of the connection area because the largest practical tip contact area will keep the dwell time to a minimum. The goal is to select a tip that will rapidly transfer heat without reacting to the solder and minimize the soldering operation dwell time.
Clean the soldering tip before and after usage, wiping the tin in a slightly damp sulphur-free sponge or dabbing it on a brass pad. After wiping/cleaning the soldering tip, always apply a fresh coating of solder to it before placing the iron in the holder.
For wire tinning, the rosin fluxes are preferred since they do not leave a corrosive residue also; if you will tin your wires, remove the dross and burnt flux from the surface of the molten solder to ensure the dross does not contaminate the items being tinned.
Aluminum to Aluminum Soldering Steps:
Based on the information presented
- We will need a high activity flux to solder aluminum-to-aluminum in electronics, and due to its corrosiveness, we must clean all flux residues after soldering. Therefore a water-soluble organic-based high-activity is a good start.
- A paste flux will work better than a liquid one since it will stay fixed to the pads, won't immediately evaporate and won't end up running to other areas.
- The solder paste selected should ideally be a high activity one and eutectic, with as large a powder size as possible. To achieve superconductivity the alloy should not contain silver or gold. If we care about magnetic interference then it should not contain nickel.
- The flux in the solder paste and the external paste flux must be compatible from a cleaning and chemical perspective.
- Both solder and flux processing windows should be compatible, ideally within the same activation range
The paste fluxes we have successfully used to aid in soldering to aluminum are No. 1260 and No. 1265 from Superior Flux with a recommended soldering range of 177-288 °C (350-550 °F)
Although not eutectic, the solder paste we have successfully used to solder to aluminum is PMS-360F-802 from SRA-Solder with an alloy melting range of 182.8-190 °C (361-374 °F).
We are currently experimenting with solder paste AL261-193-75 from Superior Flux with a recommended soldering range of 180–195 °C (356-383 °F) and an alloy melting point of 139-140 °C (282.2-284 °F).
Step 1: Bare board preheating from the bottom side via the use of a hot plate is helpful in high thermal load situations where there are no components on the bottom side of the PCB.
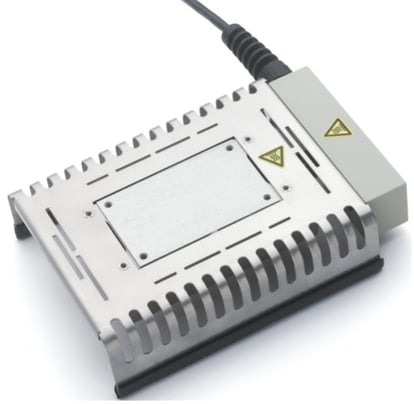
Step 2: Preclean areas to be soldered to remove dirt, grease and oil from fingerprints using alcohol or PCB cleaning chemistry. Flux doesn't clean these.
Step 3: Apply an adequate amount of paste flux. Allow the paste flux to fully cover and flow over the area(s) to be soldered in advance of the molten solder. The flux will both increase the ability of the surface to accept solder and act as a thermal transfer medium to aid in heating. This heat bridge is the most important part of soldering to aluminum. You want the volume to be enough to flood the aluminum once the flux is heated.
Step 4: Laid the NbTi wire flat against the selective copper pad.
Step 5: Apply an adequate amount of solder paste to form an acceptable solder connection by building a line of solder paste over the aluminum pad stopping where it meets the edge of the copper pad.
Step 6: Place the soldering tip into the paste flux at 380 °C (this temperature is based on the solder and flux paste we mentioned above, you would need to figure out your paste/flux process settings based on the technical data sheets of your selected solder/flux combination). The heat provided to the connection by the iron must pass through the soldering tip through the paste flux.
Do not touch the copper pads, or aluminum pads, nor the NbTi copper-coated wire.
The aluminum cannot be as hot as the paste flux, or it will oxidize. A proper solder heat bridge will maximize the heat transfer and reduce dwell time on the connection as it is being formed. You want the heat of the flux to heat the copper and the aluminum.
Do not apply force onto the soldering tip and keep it tinned before and after usage to maintain its effectiveness.
Maintain thermal contact (flux heat bridge) until a good solder spread is obtained but do not stay too long. You can achieve this by moving the soldering tip in a straight line along the path of the NbTi copper-coated wire to heat fresh flux and solder.
As the hot flux melts the solder paste, the solder is attracted toward the soldering tip, and as it moves, it wets the unoxidized aluminum, the hot selective copper and the copper on the NbTi wire. Be careful, this happens very quickly, and if the soldering tip makes contact with the NbTi copper-coated wire or the selective copper, they will conduct too much heat into the structure, and then the flux will get too hot and burn.
Step 7: Remove the soldering iron but do not disturb parts until solder solidification is complete. Hence the preference of a eutectic 63/37 tin/lead solder alloy whenever possible.
Video:
Courtesy of Alex Yarovoy
Warning:
Do not try re-reflowing the solder. If you try to repeat this process over any given pcb pad, then the paste flux will burn
Take Away:
Your product application, melting temperature and joint strength will determine the alloy selection.
However, as with any manufacturing process, the best materials, in this case, the best solder alloy and flux combination for a given application, are the ones that provide the best compromise between reliability requirements and processing requirements.
If this seems complicated, remember that application specialists at various solder and flux manufacturing companies are always willing to aid with material selection, and you can always contact Omni Circuit Boards, we are here to help.
Solder and flux manufacturing companies: